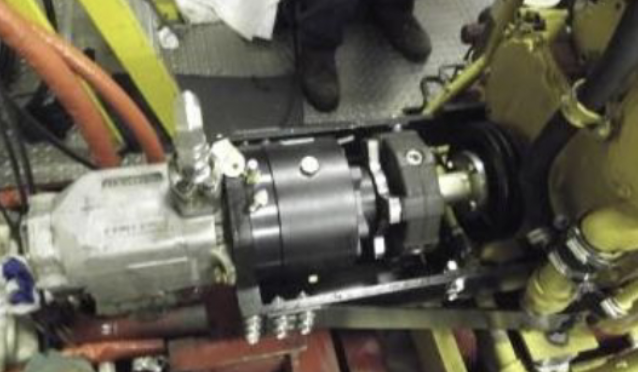
A major harbor tug operator in the US had a need to up-grade some of its old Detroit Diesel driven Gensets. This operator has the hydraulic requirements for the boat and deck winches provided by two hydraulic pumps mounted on the front of two redundant Gensets. (This is an alternate solution to main engine mounted hydraulic pumps and allows for the hydraulic systems to be run at the dock and without the mains being operated.)
In normal operation, one genset provided all of the ships power. The second genset provided all of the ships hydraulic requirements. In an emergency where additional electricity or additional hydraulic pump flow was required, the second unit could be used to provide additional resources. In the event of a failure, one genset could provide enough electricity and hydraulic flow for the boat to still operate until the first unit could be repaired, keeping a valuable piece of equipment operating and providing revenue. The clutch allowed the pump not being used to be disengaged, doubling the life of the pump and lowering the parasitic power draw from the genset engine.
The original configuration was with a mechanical Bell Housing clutch with a pump face output on the front of the Detroit Diesel. The older engines were replaced because:
- They were at the end of their useful life
- They used significantly more fuel than new modern ACERT engines
- They produced significantly more emissions than new Tier 2 conforming engines
Further, it was expected that the reduced cost to operate and maintain the new engines would pay back the acquisition cost in just a few years.
New Cat powered gensets were selected. The 1800 RPM of the new genset was higher then the 1200 RPM of the old slow turning Detroits. That change required that the pumps be replaced as well. The new genset engines were not available with optional front bell housing mounts. The customer had tried several other older design system solutions with electric clutches and drum style air clutches with speed reducing gearboxes mounted on shipyard installed fabricated beds with foot mounts. All installations suffered from premature failures due to the high torsional vibration transmitted by the new Tier II engines.
New Logan Clutch front mount PTO kits were also selected. The Logan Clutch front mount kit provided a lot of advantages over the old configuration.
- Remote activation from the helm simplified with standard pneumatic controls.
- Logan Clutches that are self adjusting for wear meant ZERO adjustment maintenance during service life.
- Kit/bracket pre-engineered package kept installation time in yard and custom fabrication requirements to a minimum.
- Integrated torsional coupling for torsional vibration resistance.
- System entirely mounted to the engine keeps all components attached to the engine vibrating together and not rigidly mounted to another component further reducing susceptible to torsional vibration wear.
- 100% of rated torque can be taken from front of engine through clutch.
- Clutches rated for 100% duty cycle guaranteed long life in a demanding application.
Installation was successfully completed in just a few short days without a haul out.
After several years of operation there has not been any downtime due to torsional failure. The Logan systems have been so much more reliable than any of the others, that several “new” alternate designs have been replaced with Logan Clutch front mount kits.