Screw Machine Controls
Affordable Technology For Your Screw Machine Simplify Screw Machine Operation Without Going Overboard Or Over Budget
The CS2001 XT is specifically designed to bring new machine technology to your existing fleet of screw machines. With features such as Tool Counters, Thread Check, Machine LockUp Detection, Stock Load and more, the XT offers screw machine users more flexibility during set-ups, and increases overall machine productivity.
Realize significant productivity gains utilizing the same operator, machine and floor space.
OEM, Factory or Field retrofitted; the CS 2001XT is the right technology for your screw machine. Available for Acme-Gridleys, Wickmans, Davenports and New Britains.
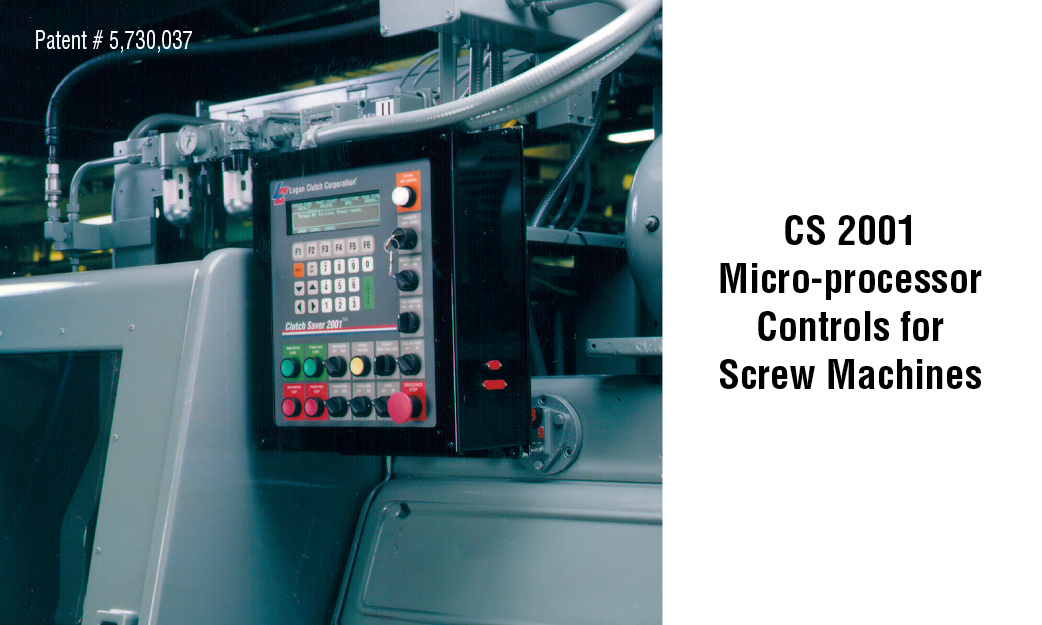
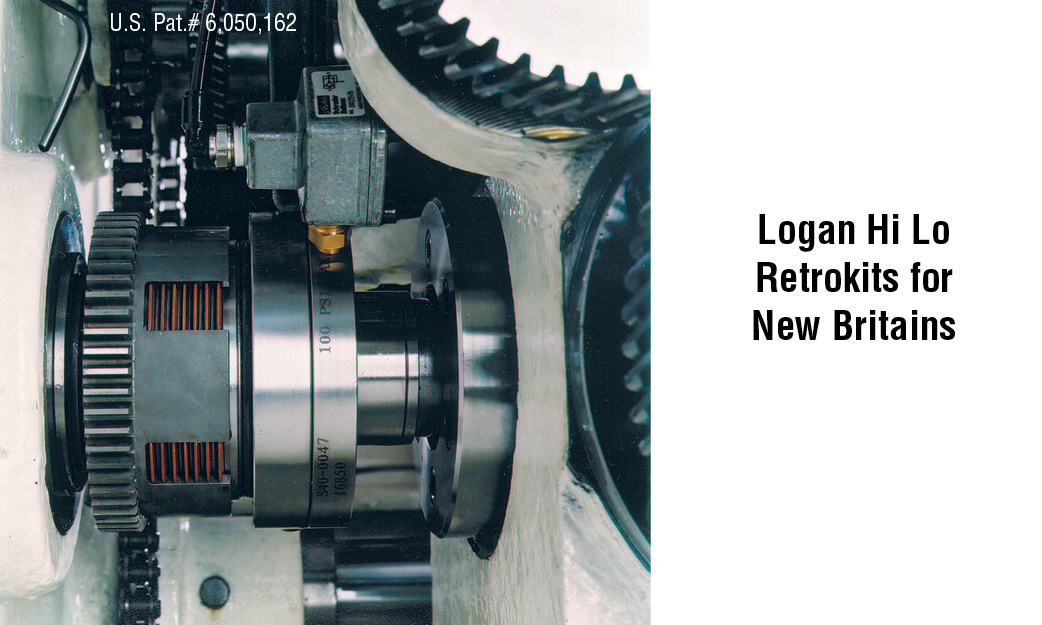
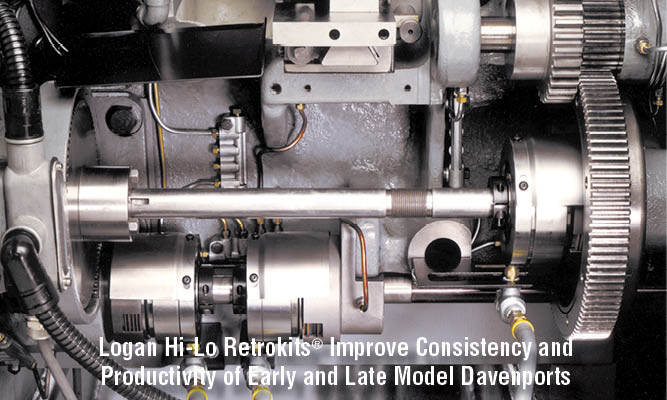
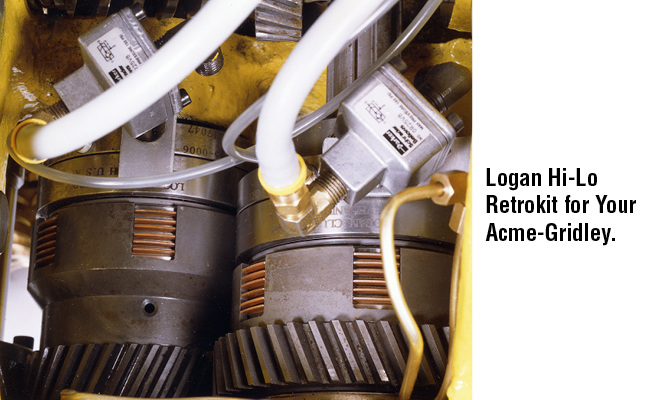
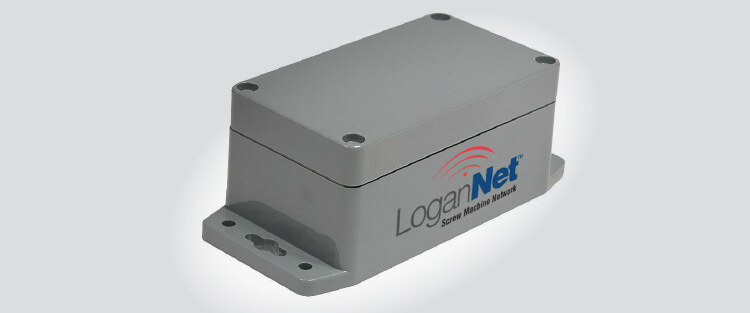
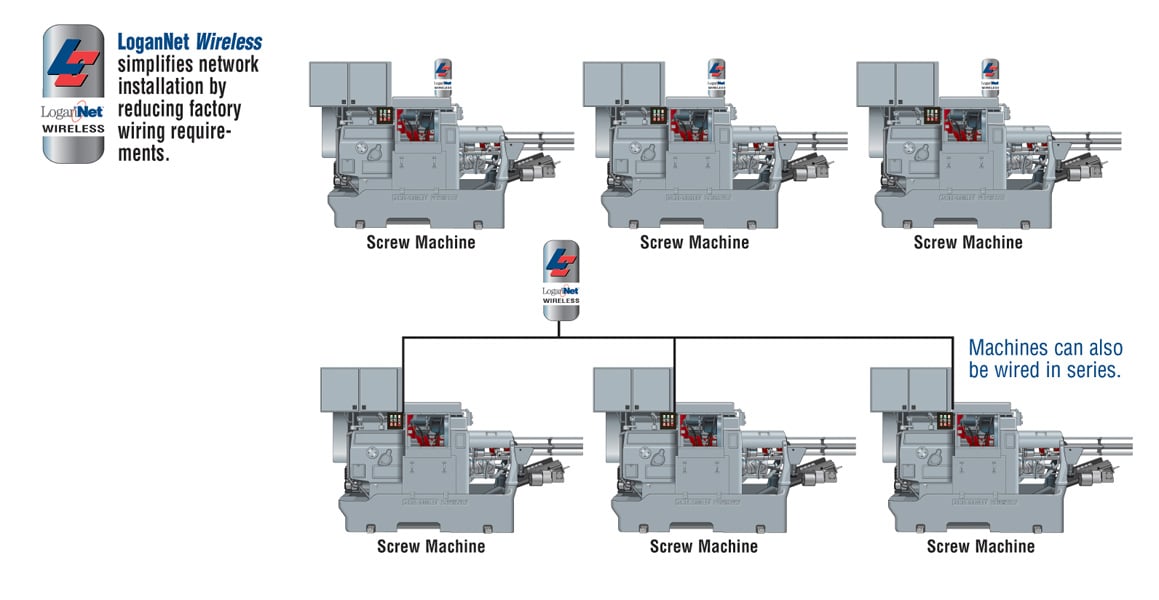
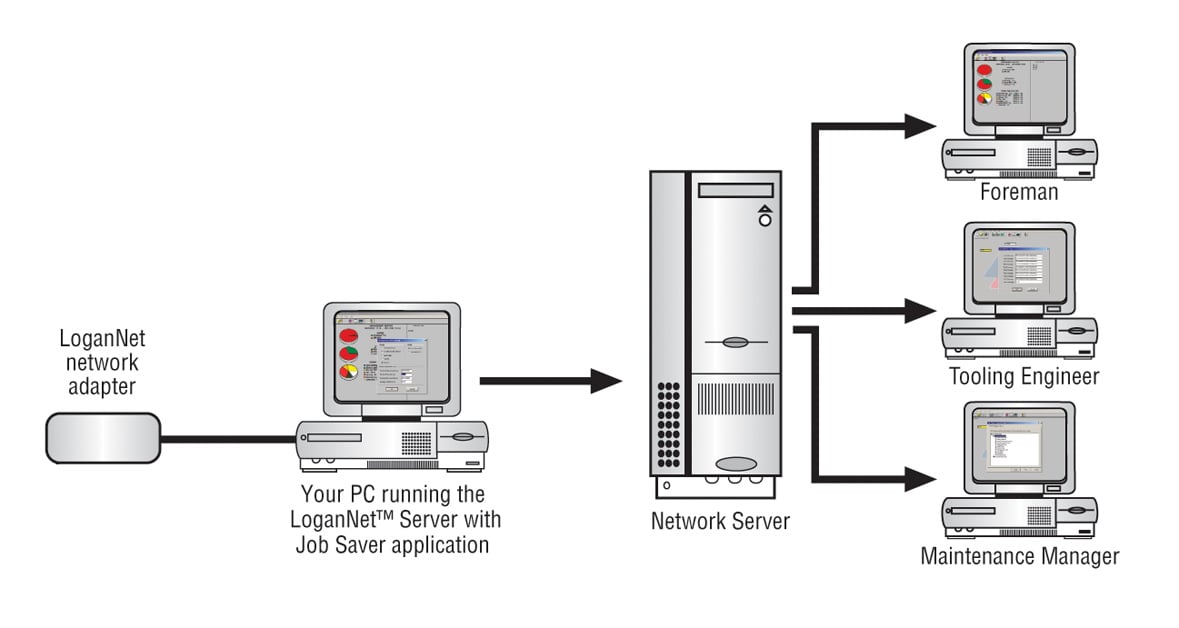
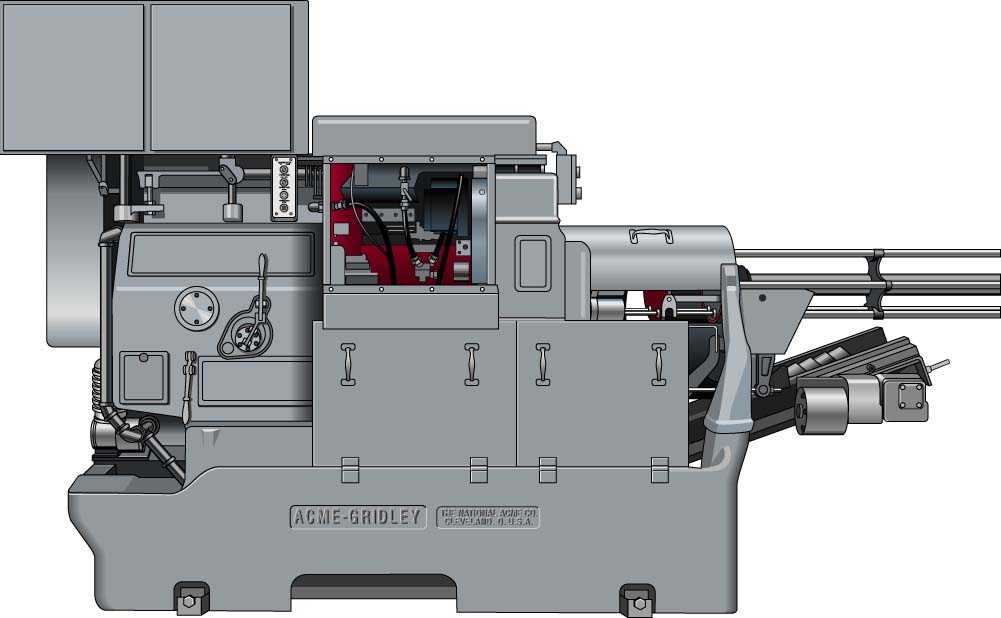
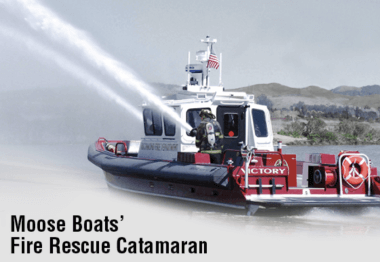
Improves Machine Operation and Productivity
- Machine LockUp Detection Minimizes tool crash damage.
- Improve Cycle Time Program high and low speed shift points in degrees.
- Easy to Read Screen Displays cycle time, parts count, parts per hour,accumulated run-time and machine positionin degrees or hundredths. Useful during setup, roubleshooting and training of operators.
- Thread Check - Detects tap failure, stopping the machine prior to machine index.
- Stock Load Positioning- Eliminates jogging. Automatically positions the machine for bar loading.
Reduces Set-up Time
- Up to 15 Programmable Tool Counters - Maximize part finish. Reduce perishable tooling costs.
- Auxiliary Outputs - Eliminate auxiliary cams & limit switches associated with attachments.
- Programmable Air Pick-Off Collet - Opens and closes collets in degrees.
- Interfaces with Popular Barfeeders and Loaders - Accurately Positions machine in "bar load window" to accept bar stock every time.
- "Stock Load" Feature reduces manual stock load time / jogging up to 50%.
- Security Key Protects Set-Up Parameters.
Factory or Field Retrofitted - Install an XT right on your shop floor or specify during rebuild. Field Service is also available.
Extended Warranty - Ask about our extended clutch warranty when you purchase an XT along with one of our Hi-Lo Retrokits.
New Technology - Enjoy New Machine technology with your existing equipment.
Standard Logan CS 2001XT Control
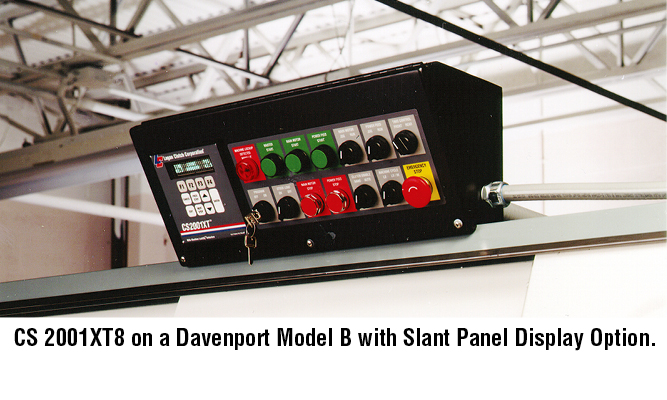
Features and Their Benefits
1. Machine Lock-up detection: Detects main drum shaft rotation and shuts down your machine if a lock-up condition occurs. Minimizes damage to clutches etc.
2. Reduce Cycle Time: Program the high and low speed shift points in 1-degree increments, giving the operator more set-up flexibility without having to mechanically re-time the high speed and brake cams. Reduces possibility of going past low point in the high-speed cycle. Go into high speed early or later if your layout completes the machining cycle before or after high point.
3. Fifteen Programmable Tool Change Counters: Shuts the machine down at designated tool service time; minimizing tool changes and maximizing quality finishes and threads. 10 counters are designated for fatal errors, thus stopping the machine; and 5 notify the operator of a tool change, but do not shut the machine down.
4. Programmable Air Pick-off Point: Program the opening and closing of air pick-off collets in degrees. Eliminates mechanical adjustment of Cams. (Additional hardware may be required for Davenports).
5. High Point / Low Point Reference: Automatically stops the machine close to high point or low point. By hand cranking the machine, the operator will confirm the exact high or low point by the display monitor. Useful during set-up, eliminates dial indicator.
6. Easy to Read Screen: Displays cycle time, parts count, parts per hour, accumulated run-time and machine position in degrees. or hundredths. Useful during set-up, troubleshooting and training of operators. (Davenport users have the option to read machine position in hundredths).
7. Revisable Parts Counter / Job Counter Display: Makes it possible to change the counter display. Useful during stock-up, enabling the operator to correct the parts count as needed.
8. Stock Depletion: Takes intelligent input from your stock depletion sensor and shuts down the machine when the bar stock becomes too short to feed out to length.
9. Tapping Right Hand / Left Hand Select: Makes changing from right hand tapping to left hand tapping as easy as pushing a button.
10. Thread Check/Tapping Failure Detection: Shuts the machine down if the tapping cycle does not complete before machine index. Prevents parts without threads, sorting costs etc. (Additional hardware may be required for Davenports).
11. Stockup Mode: Automatically stops the machine in the correct position for material loading.
12. Programmable Air Blast: Allows the operator to program the exact time to blast air to the part for chip cleaning; saving compressed air for other uses.
13. Alarm Message Display: Display gives descriptive message of any alarm message that occurs, or causes the machine to stop. Saves messages in series for diagnostic review.
14. Start Interrupt: Shuts machine down if an interlock sensor is faulted.
15. Eight Auxiliary Outputs: Eliminates cams, limit switches and bracket fabrication associated with attachments. Allows operator to program, in degrees, the engagement and disengagement point of attachments, such as broken tool, short part detectors, thread rollers, bar loaders and feeders into the machine cycle. Outputs are capable of operating twice within the machine cycle, (Ideal for slowing the machine down during bar feed out).
16. Ideal for bar Loaders: Intelligent input for bar loader and bar feeder integration. Accurately positions machine in "bar load window" to accept bar stock every time.
17. Chip Breaker Feature Option: Avoid the nesting of metal stringers that require a machine shutdown to remove. Use this feature to maximize machine up-time and production. The new chip breaker feature sets the point in degrees or hundredths where the machine will pulse the feed according to the chip dwell and chip pulse.
Contact Our Sales Team
Our Sales Engineers can help you find the exact product or service you need to succeed.