Logan Generation III Air Pick-Off Attachments
For Your Screw Machine
New Logan Generation IIITM Air Pick-OffTM Attachments
Save Time, Money, Reduce Costs
New Logan Generation III Air Pick-off Attachments eliminate secondary machining operations and increase the productivity of your early and late model screw machines - while utilizing the same operator, machine and floor space.
Pickup and Cut Off a Longer Part: Eliminate Secondary Operations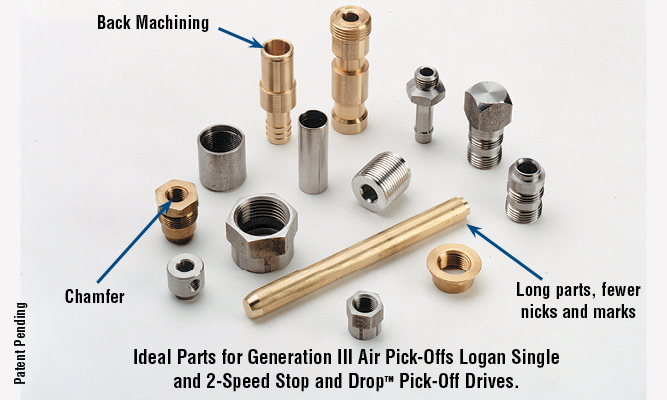
The Logan Generation III assembly is almost 2 shorter in axial length in the tool zone than conventional OEM and after market air pick-off attachments. Now you can pick off longer parts, eliminating secondary back chamfering, forming and drilling operations.
Improves Accuracy, simplifies pick-up stop adjustment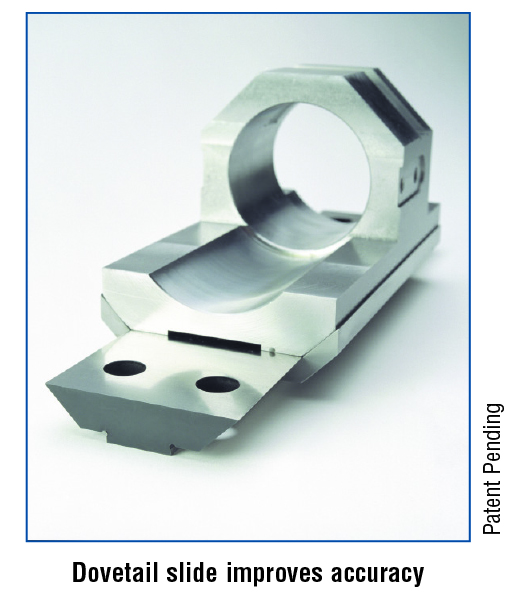
Our new Dovetail slide mounting design maintains accuracy for a longer period than Generation II box slide designs, and uses a composite material to provide freer slide movement. Minimizes chip skiving too.
Lower Tooling Costs
More standard length tools can be used on the back finishing slide -
lowering tooling costs. Current methods may call for special tools to be shortened in order to fit longer parts into the tool zone. Standard tools can be used in the back finish tool holder to reduce perishable tooling costs.
Minimize Tool Breakage
More space is available to clear tooling - minimizing tool breakage during machine index
New Logan Generation III Air Pick-Off Design Features and Benefits
Advantages:
-
2" Shorter Axial Length: In Many cases the Logan Generation III attachment is almost 2" shorter in axial length than existing attachments on the market. Now you can pick off longer parts, eliminating a secondary back chamfering, drilling or machining operation.
-
Stronger Work Spindle: We've replaced present work spindle ball bearing with a needle bearing to improve rigidity for stronger side or radial loads from tools Making your pickoff spindle more like a work spindle.
-
Dovetail Slide Improves Accuracy: New Dovetail slide maintains accuracy longer and has freer slide movement vs. current box slide. More aggressive metal removal is now possible. Composite slide material enables freer slide movement and minimizes chip skiving.
-
Advanced Lubrication System Increases RPM Capabilities: A dedicated lubrication line to the housing assembly provides higher RPM capabilities improving part finishes and bearing life.
-
Heavy-Duty Viton O-Rings and Seals: Viton O-Rings and Seals are designed to withstand todays sulphur based and water based cutting fluids for longer periods than traditional seals used in Generation II units.
-
New Bearing Locknut Preloads High Precision Angular Contact Ball Bearings: The new Logan Generation III pickoff uses a bearing locknut to preload and position new high precision angular contact bearings. Current Generation II design uses retaining ring to hold a double row ball bearing in place in the pick-off housing. This retaining ring fails prematurely, increasing downtime and maintenance.
Benefits:
-
Eliminate Secondary Operations - Pick-off longer parts: Save Time and Money by eliminating secondary operations. More complex parts and parts families can now be run on your machine eliminating back drilling, back chamfering, and machining operations.
-
Lower Tooling Costs: Standard length tools on the back finishing slide can be used since more space is available thus lowering tooling costs. Current methods may call for special tools that are shortened in order to "fit" longer parts into the cycle.
-
Reduce Down Time: 2-piece construction enables removal and re-installation in half the time of conventional 1-piece Generation II Pick-offs.
-
Reduce Set-Up time: Stop rod location enables operator and set-up person to adjust right in the tool zone current methods call for adjustment in the gear box.
* Available for Synchronized and non-synchronized gear trains. Specify pickoff gear configuration at time of order.
* Camless Feature also available. Contact Logan for details.
|
Positive Stop Rod Simplifies Adjustment
Positive Stop Rod for Accurate Positioning
The Generation III Positive Stop rod is positioned in the tool zone, rather than in the gearbox. Adjustments can be made in the tool zone within view of the desired pick-off collet position allowing for a more precise stop setting. Our stop rod feature enables operators to hand adjust pick-up stops right in the tool zone rather than in the gearbox, simplifying adjustment and increasing accuracy.
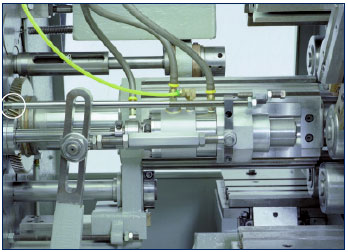
Advanced Lubrication System Increases RPM Capabilities
A dedicated lubrication line to the housing assembly provides higher rpm capabilities - improving part finishes and bearing life. Heavy-Duty Viton O-Rings and Seals are incorporated into the pick-off spindle housing to ensure longer life in todays sulphur and water based cutting fluids.
Makes Pick-off Spindle More Like a Work Spindle
Stronger thrust bearings in the work spindle enable up to 10x more axial or radial loads from tools than conventional Generation II Air Pick-offs; turning your pick-off spindle into a true work spindle. The Logan Generation III uses a bearing locknut to pre-load and position new high precision angular contact bearings in the pickoff spindle housing. (Generation II pick-offs use a retaining ring which fails prematurely under moderate load conditions).
Two-piece construction simplifies installation and maintenance
Our 2-piece constructed shaft enables users to remove and re-install their Logan Generation III Pick-off in almost half the time of conventional one-piece construction air pick-offs. Plus, our split-style center drive gear design eliminates the need to pull the center drive shaft from your machine shortening the installation process. O-Ring Grooves and Seal surfaces have an ideal radius to minimize pinching and shearing during installation.
Simple to Install:
Each Logan Electrical, Mechanical, Pneumatic and Accessory kit is designed to save you time and money during installation. Kits are furnished with detailed mechanical, electrical and pneumatic schematics.
-
Easily retrofits older machines.
-
Field installation service is also available.
Air Pick-Off Case Study
The Problem:
JUST IN TIME "J.I.T." PLANT ENCOUNTERS BOTTLENECK
Many J.I.T. manufacturing facilities follow a simple guideline: "Parts made that day must ship that day". A major J.I.T. Manufacturer of Hydraulic Fittings encountered a bottleneck in its secondary chamfering operation for a hydraulic hose fitting on a 1-1/4 RB-8 Acme-Gridley. The bottleneck extended lead-time beyond the 1-day turnaround for production - increasing part cost.
The Solution:
The Customer installed a Logan Generation III Air Pick-off and Back finishing slide. The fitting is now chamfered during the last operation in the machining cycle on the Acme-Gridley thus eliminating the need for the secondary operation.
FURTHER OPTIMIZATION:
The Customer added a Logan XT16 control and 1- speed pick-off drive brake. The control enables the set-up person to set the air pick-off collet opening and closing sequence in degrees; program an air blast to clear chips, and stop the spindle just prior to the collet opening; eliminating nicks and marks on the part during the part ejection phase from the collet.
THE ADVANTAGE:
Logan delivered a solution, which eradicated (2) handling operations at a minimum projected cost of .085 cents per operation plus eliminated extra handling in the queuing area for secondary cleaning and inspection. (See table below).
The person performing the secondary operation was now able to perform other value added duties within the plant.
THE MATH:
.085 cents per operation x 2 operations = a .17 cent savings per part, or approximately $ 71,604.00 per year. The Return On Investment, (ROI) was recovered within 3-4 months of the installation - and that's taking into account only 2 of the 5 steps eliminated.
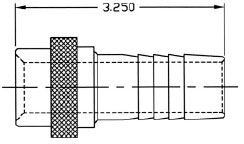
THE OLD 10-STEP PROCESS:
- Part is machined without back chamfer on an Acme-Gridley
- Counted
- Cleaned
- Inspected
- Handling to secondary station
- Back chamfering operation is performed
- Counted
- Cleaned
- Inspected
- Shipped
* Secondary burring machine is set up between 5th and 6th step to run the job
THE NEW 5-STEP PROCESS:
- Part is back chamfered utilizing a Logan Generation III Pick-Off and back Finishing Slide during the manufacturing sequence on a 1-1/4 RB-8 Acme-Gridley
- Inspected
- Cleaned
- Counted
- Shipped
IMPORTANT: No increase in cycle time was realized since the XT control improved machine high and low speed changes in 1-degree increments.
Logan Air Pick-Off Justification Worksheet
ACME-GRIDLEY 1-1/4 RB-8 |
PRODUCTION
|
SAVINGS |
---|---|---|
Cycle Time |
16 Seconds |
Secondary cost savings |
Parts per minute (x 0.72) | 2.70 | .46 Per Minute |
Parts per hour | 162.00 | $27.54 Per Hour |
Parts per shift (10 hours) | 1,620.00 | $275.40 Per Shift |
Parts per week (5 days) | 5 | $1,377.00 Per Week |
Parts per year (52 weeks) | 52 | $71,604.00 Per Year |
Production Time = 10 hours / Day (72% Efficiency or Run Time) Secondary Operation Cost =
.085 cents per operation x 2 handling operations = .17 cents
Logan Air Pick-Off Control Options
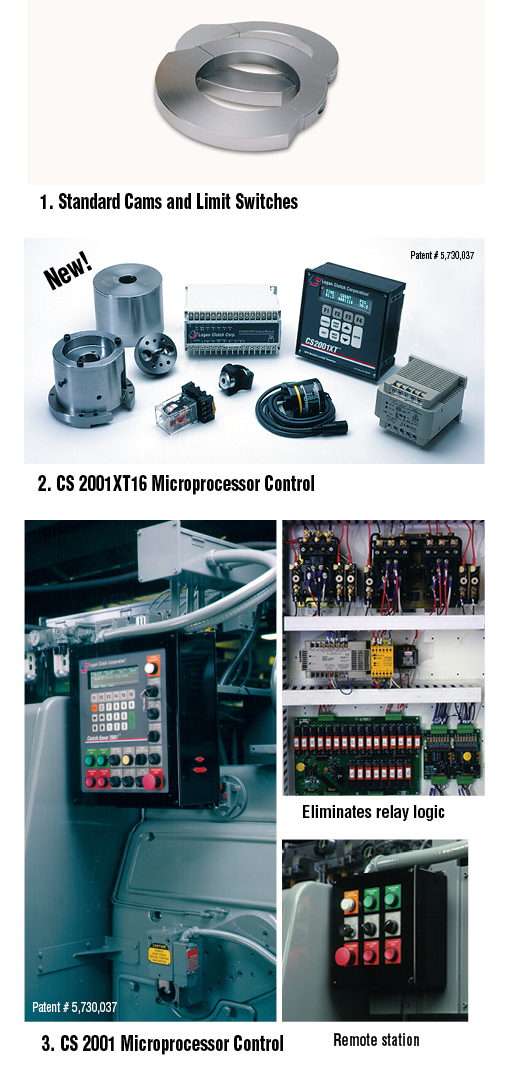
1. Standard Cams and Limit Switches
Feature
-
Conventional Cam and limit Switch operation
2. CS 2001XT16 Microprocessor Control
Popular Features
- Easy to read 2-line screen Displays cycle time, parts count, machine position in degrees
- Machine Lockup detection -
- low-speed shift points in degrees
- Thread Check - detects tap failure and shuts down your machine before index
- 15 programmable tool counters
- Eliminates auxiliary cams and limit switches
- Stock Load positioning - reduce stock-up by 50%
3. CS 2001 Microprocessor Control
All the features of the XT16 plus:
- Full pre-wired push-button control station
- Eliminates relay logic
- 35 Programmable Tool Counters
- Air coolant, lube pressure monitor capability
Plus many more features!
Contact Our Sales Team
Our Sales Engineers can help you find the exact product or service you need to succeed.