Hi-Lo Retrokit Davenport
For Your Davenport Model B
Optimize Your Model B! New Logan Hi-Lo Retrokit® with Lock-up Detection and Controls!
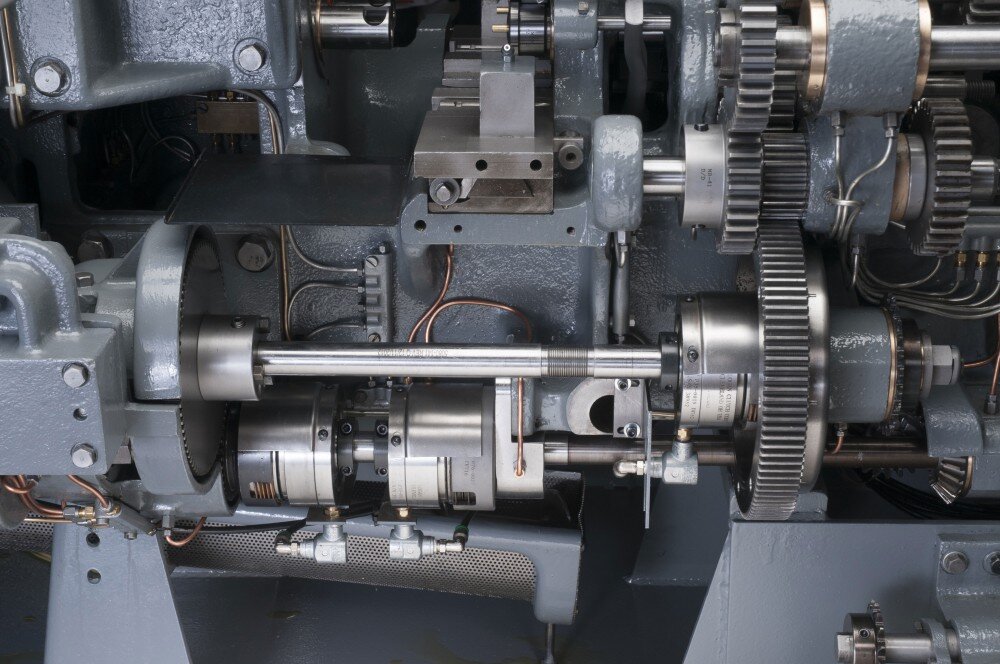
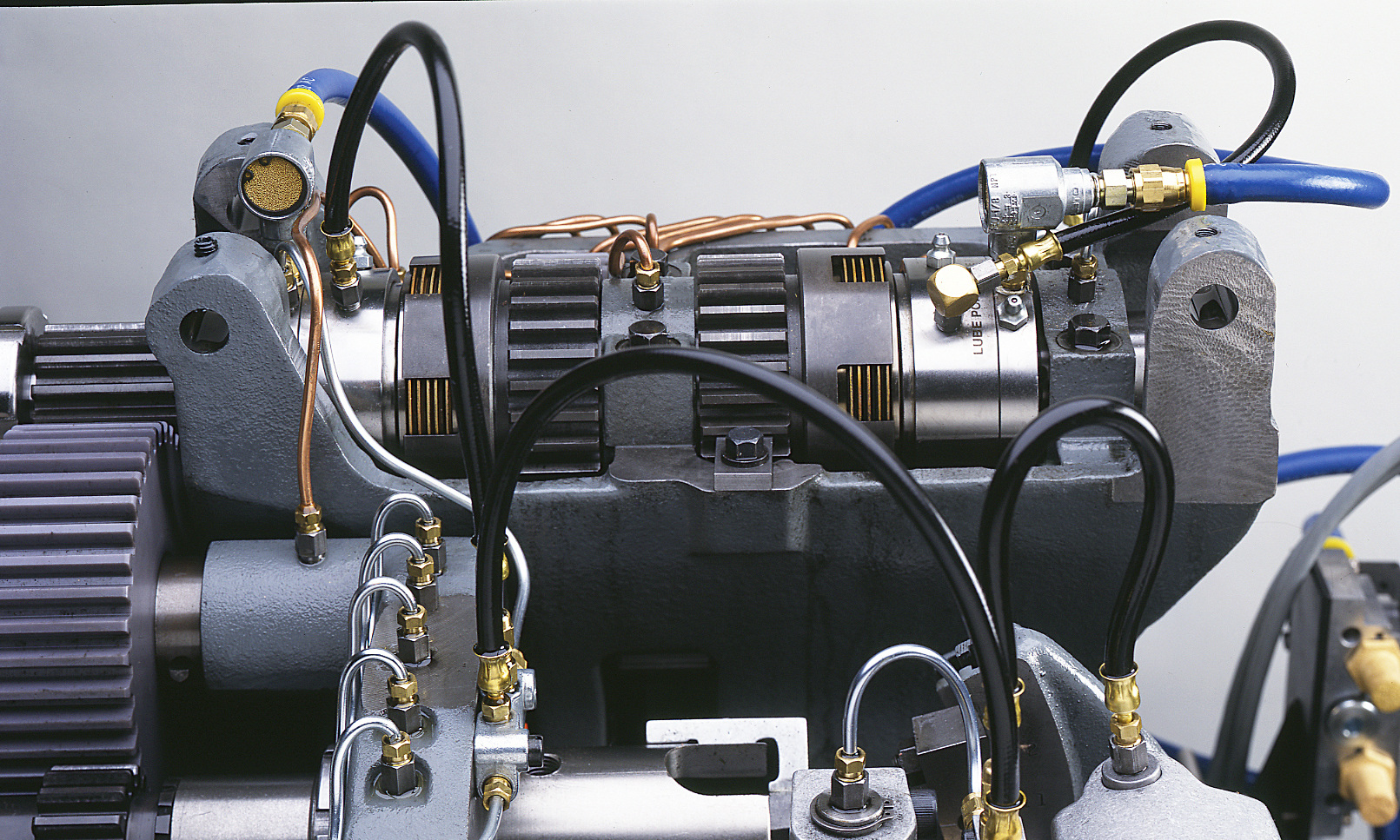
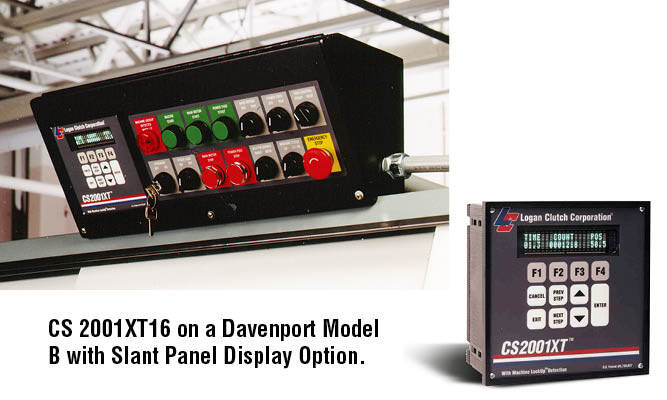
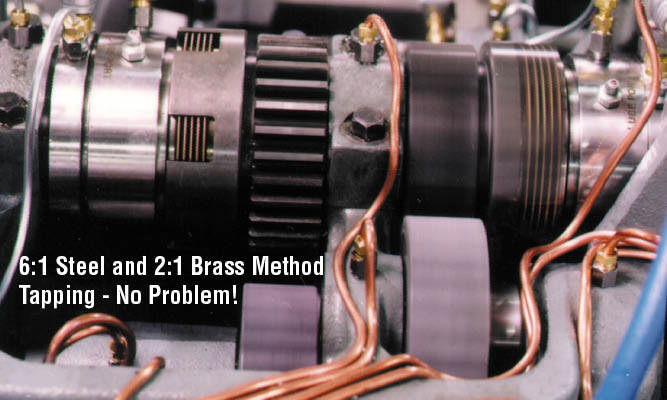
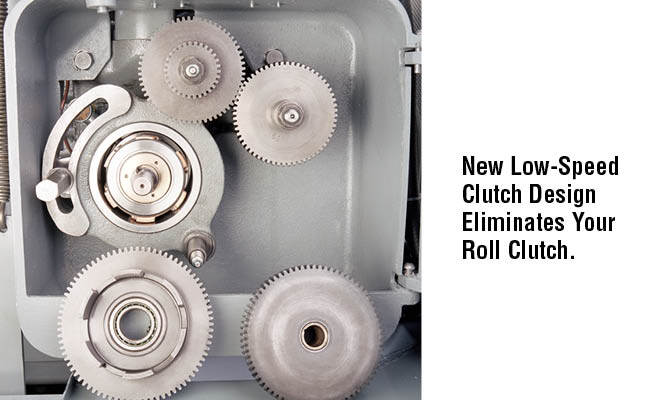
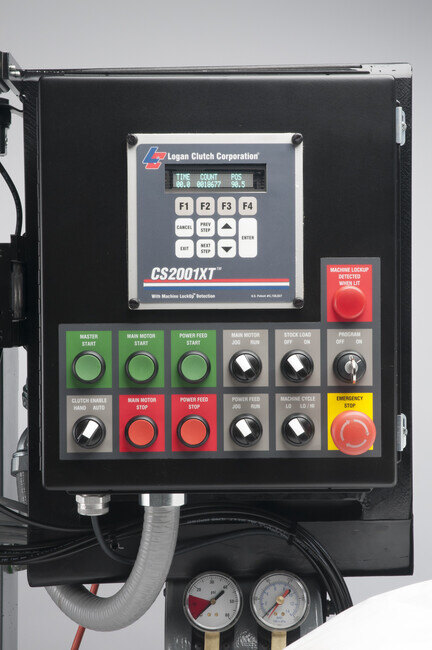
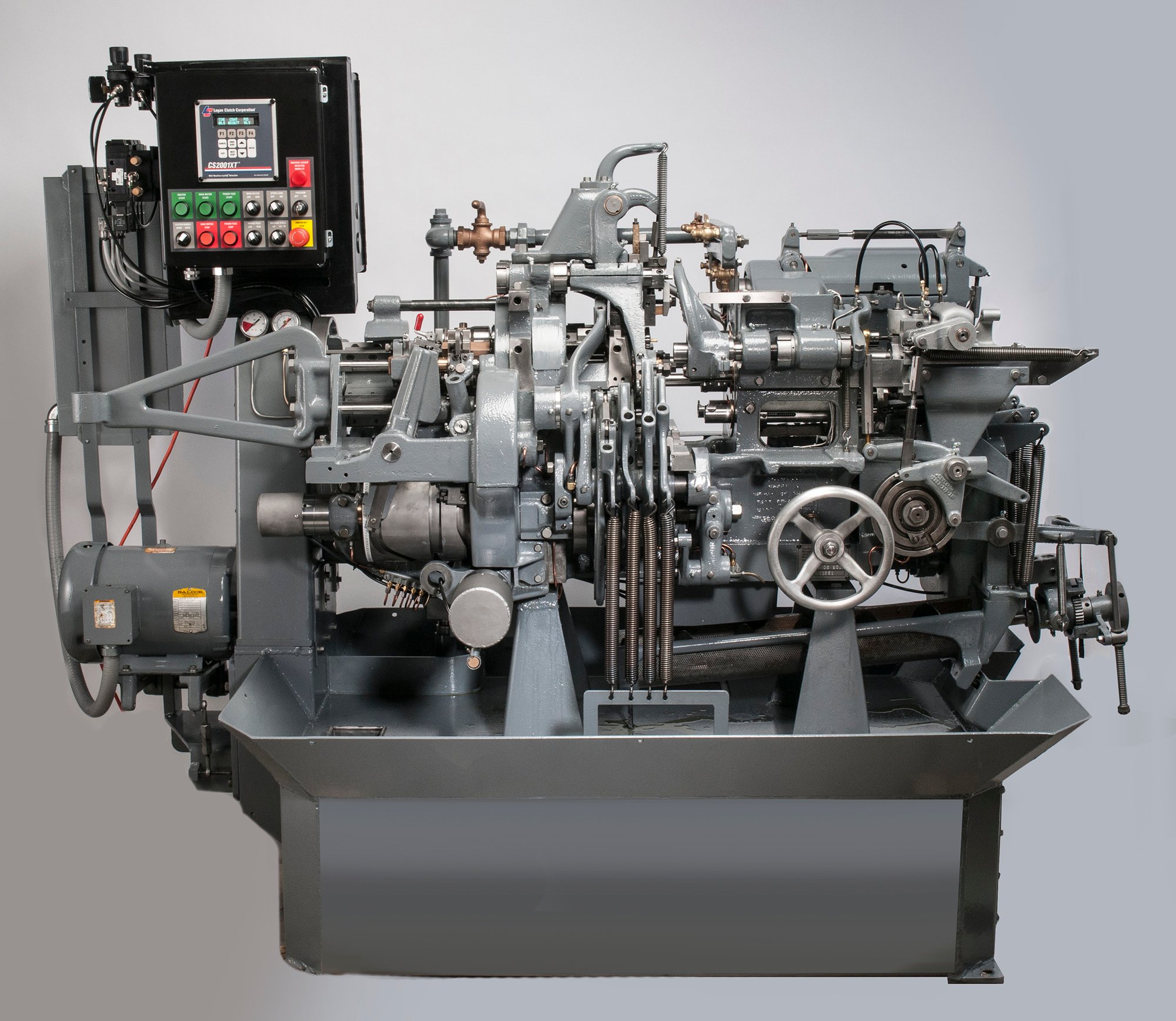
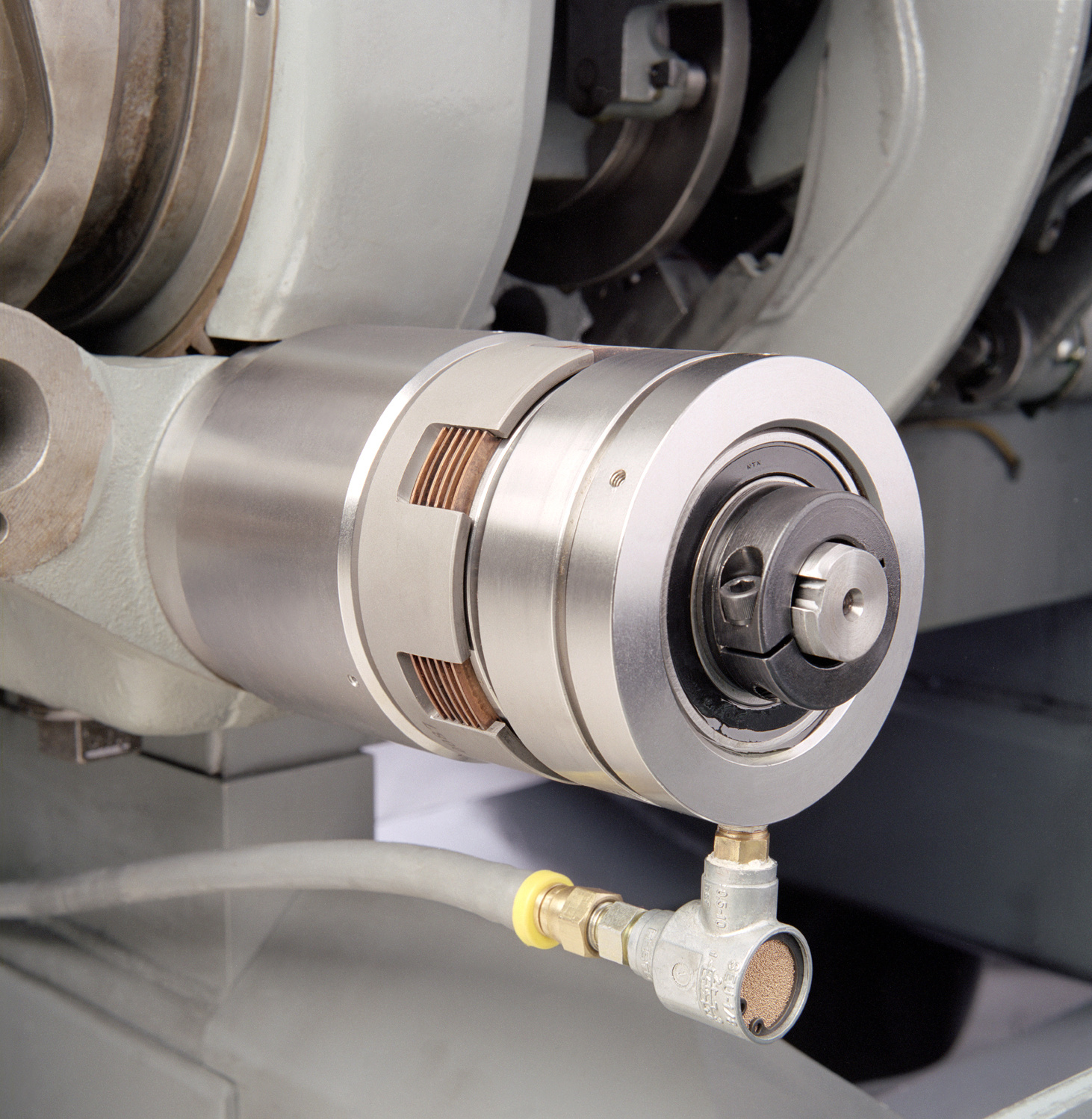
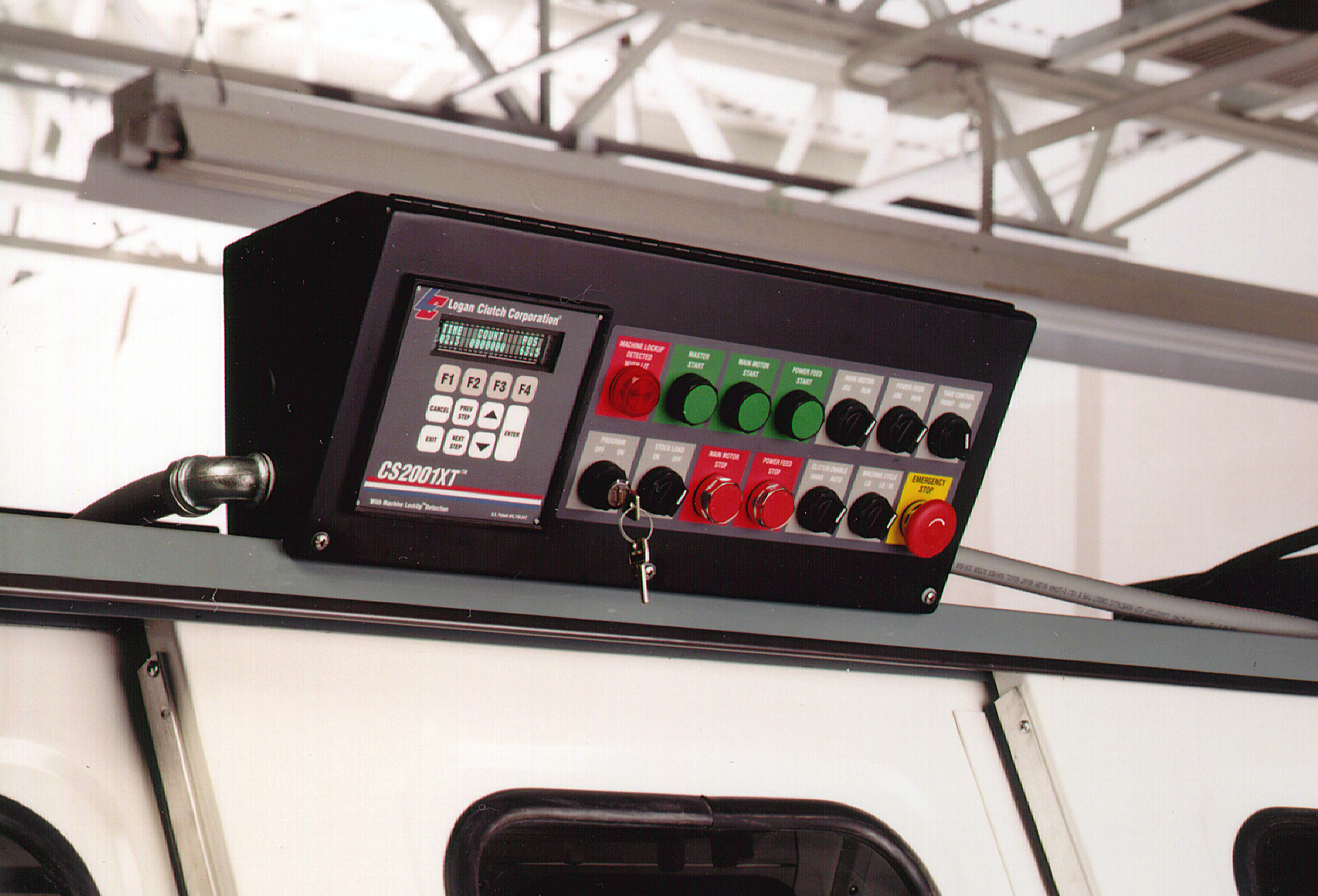
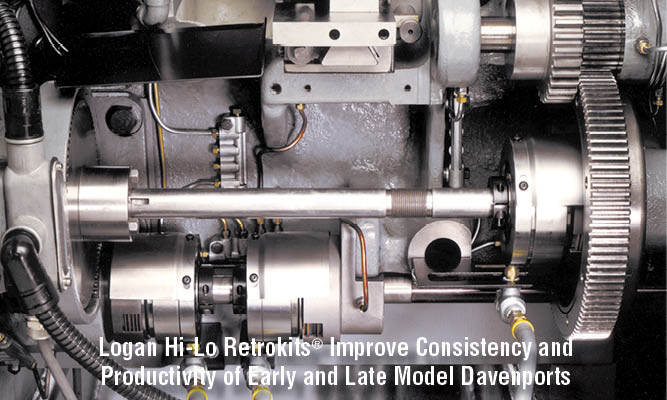
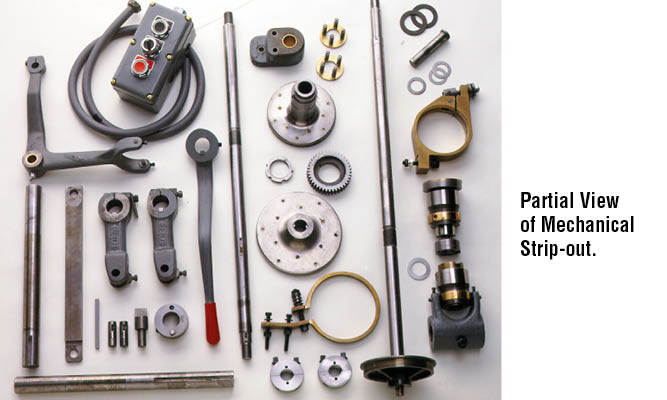
Cycle time on a conventional Model B can vary 3-4 tenths of a second or more.
This variation occurs due to an improperly over or under adjusted mechanical high-speed clutch, starter clutch or band brake. For example, if your cycle time on a job layout is planned at 2.0 seconds, you are more than likely losing 10% or more in productivity, or almost 200 parts per hour - with only 2 tenths variation in cycle time! Logan can guarantee cycle time repeat- ability over millions of parts, all without ever stopping the machine to mechanically adjust a clutch or band brake. Even better, if your layout completes the machining cycle in less than 50 hundredths, your set-up personnel can adjust the high and low shift points in degrees or hundredths to speed up the job.
Roll Clutch Removal Increases Productivity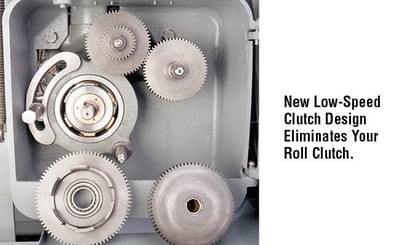
Mechanical Roll or “Rollaway” clutches have a tendency to slip and grab at different points during speed changes and indexes - causing expensive tool breakage and downtime when the machine goes past low-point in high
-speed. Since Logan clutches improve cycle time repeatability, our low-speed clutch replaces the old-style roll clutch and enables set-up personnel to position tools closer to the work-piece, further reducing dwell time and overall cycle time.
Roll Clutch Removal
- Cycle time repeatability within tenths of a second over millions of parts.
- Reduces possibility of going past low-point and crashing tools during the high-speed cycle.
- Eliminates maintenance and downtime related to roll clutch adjustment.
- Field retrofits with existing Logan Retrokits.
View of a typical Davenport timing chart. As you know, Davenports rotate counter clockwise. The Logan Hi-Lo Retrokit enables your Davenport to enter into high speed a few degrees earlier (55 degrees vs. 60 degrees) and stay in high longer (95 degrees vs. 92.5 degrees), thereby allowing your machine to “get back into cut” much faster. It takes less time to get back into the cut, over a period of millions of parts – which increases your machines overall productivity using the same operator, machine and floor space.
Overall, these basic speed changes enable your Davenport to improve cycle time by 10%, and sometimes more depending upon the job.
Here are some other areas of savings based on user reports:
1. Speed and consistency of index.
2. Can be adjusted to any shift point (on-off) to optimize work cycle time.
3. No end thrust on starting and high-speed shafts, drastically decreasing the need for maintenance.
- Taper cone bearing
- Thrust washers
- No rolls and pins
- No shifting shoes and pins
- No high speed cam to wear out
- No high speed lever to adjust
- No chucking mechaniziums to grease
- No levers and pins to break
- No engaging sleeves to wear out
- Will not pop out of gear
- No rolls to wear out in roll clutch
4. Snuber brake mounted on high speed shaft eliminates the need for a mechanical one
- No need for adjustments
- Does not pull down on 5080-20-10 shaft
- Will not wear out $500.00 bronze worm gear
- Will not wear out cam carrier bushings
- Can be applied as needed throughout the work cycle for drastic drop off cams
- Is only applied when needed saving on electricity cost, decreasing load on electrical components.
Additional parts produced per year - with Hi-Lo Retrokit 700,000
Total added revenue to company’s top line, utilizing existing machine, operator and floor space $42,000.00
Shown calculation is based on 10% increase in productivity - Varies by machine vintage
Hi-Lo Retrokit Leads to New Control Capabilities
Now that your machine is equipped with a Logan Hi-Lo Retrokit, integration of simple, efficient controls is a breeze. That’s why we now include our CS2001XT16 as standard equipment on all factory supplied Logan Model B Hi-Lo’s. The XT16 displays cycle time, machine position in degrees or hundredths, and enables you to electronically program attachments and devices normally operated by cams and limit switches. This leaves you room to easily expand into more productivity enhancements such as broken-tool, short- part detectors, bar loaders and feeders. Call Logan for more details.
- Achieve maximum torque with our High-CapacityTM starting clutch.
- Self-adjusting disc pack guarantees cycle time repeatability. Eliminates the need for mechanical adjustment.
- Quick-stop, power-applied brake. Ideal for bar loader applications.
Hi-Lo Retrokit Features:
- Replaces mechanical clutches, band brake and linkages with fast-acting, air-actuated Logan Clutches.
- Positive, fast-acting Logan Clutch engagement guar- antees more consistent cycle time repeatability than conventional mechanical clutches.
- Simplifies clutch and brake maintenance. No over or under adjusting of clutches and band brakes.
Savings
- Increase overall machine productivity from 10- 20%.
- Reduce cycle time - Tools can be positioned closer to the work piece due to repeatable high and low- speed clutch-engagement.
- “Go To” Stock Load positioning feature reduces manual stock load time by 50%. Also minimizes cut-off tool breakage.
- LockUp detection feature - detects main drum rotation and shuts down your machine if a lock-up condition occurs.
- Better machine utilization - More productivity from existing machines, operators and floor space
New CS2001XT16 Control - No Programming!
Popular XT16 Features
- Plug and play - No programming required.
- Easy to read screen - Displays cycle time, parts count, and machine position in degrees or hundredths.
- Improve cycle time - Program high and low-speed shift points in 1 degree increments.
- Auxiliary outputs - Eliminate auxiliary cams & limit switches associated with attachments.
- Programmable job counter - Counts machine indexes or interfaces with short-part or feed sensors.
- Security key protects set-up parameters.
- Easier to teach - Simplifies machine operation.
- Pre-wired, push-button control station makes installation simple and efficient.
plus many more features - call for details
Simple to Install - Factory or Field Retrofitted
Each Logan Electrical, Mechanical, Pneumatic and Accessory kit is designed to save you time and money during installation. Kits are furnished with detailed mechanical, electrical and pneumatic schematics.
- Easily retrofits with older machines
- Field service is also available
Call today for your FREE Logan Hi-Lo Retrokit justification worksheet or visit our Hi-Lo Retrokit Savings and input your own production data.
Contact Our Sales Team
Our Sales Engineers can help you find the exact product or service you need to succeed.