CS2001 Clutch Saver
CS2001 Clutch Saver
Modernize Your Screw Machine
Unprecedented Operating Flexibility - Simplifies set-up and increases productivity. The diagnostic screen display reduces downtime through quick and easy troubleshooting.
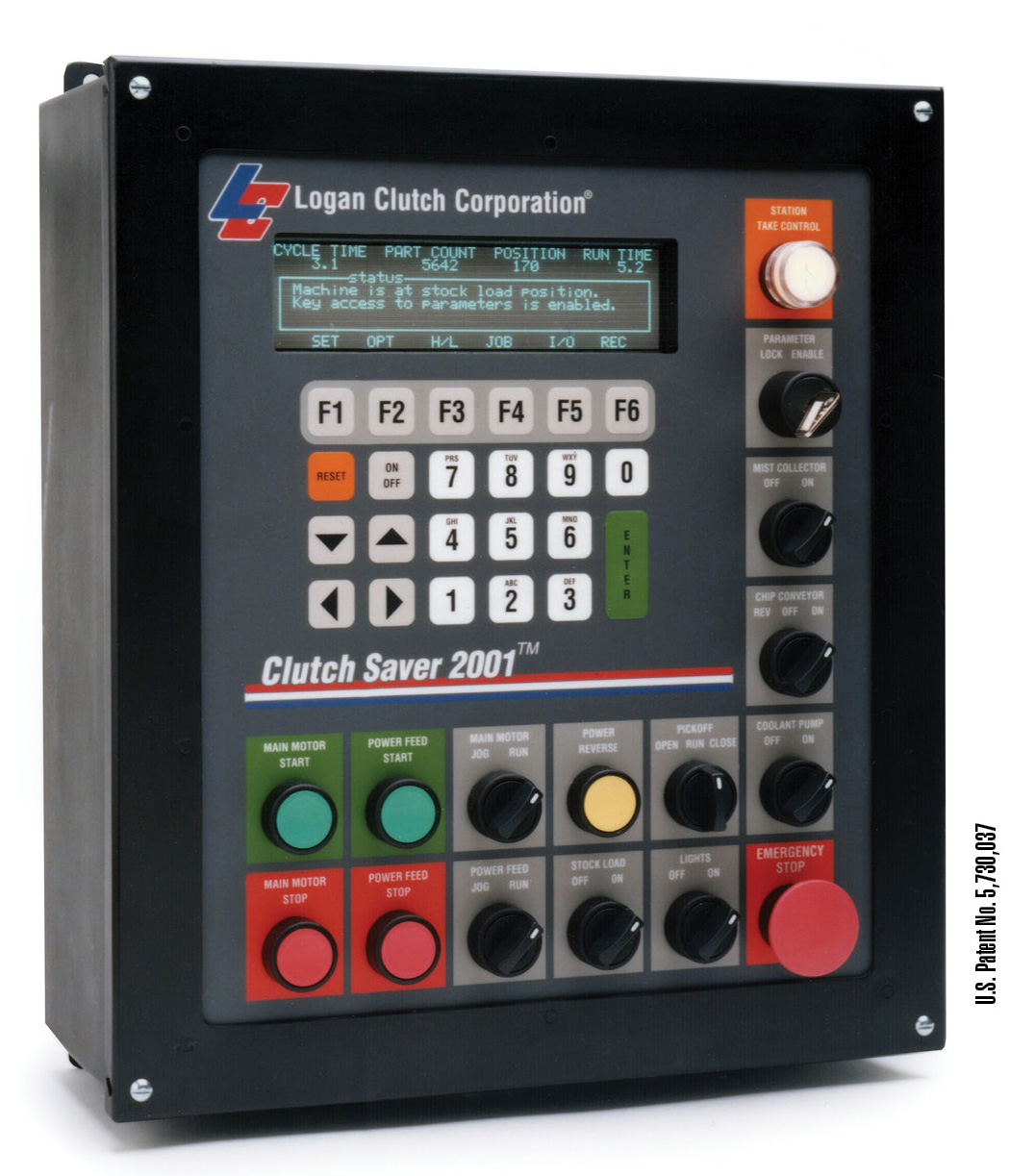
How it Works - The patented CS 2001 goes far beyond simply modernizing screw machines. The C
S 2001 monitors the drum shaft position in real time (within 1/3 of a degree) with an absolute shaft encoder. Using the touch pad, operators and set up people can enter positions for high point, low point, pick-off point, thread check, and other important settings, and view the new settings right on the screen. The CS 2001 is operator friendly by utilizing familiar selector switches already in use in your day to day operation.
Optimizes set-up, makes short run jobs more economical - Shift points can be set at optimum positions by using the display window - no more settling for shift points that are “close enough”. Overall set-up time is further reduced since high speed and brake cams do not need to be re-timed. Engagement points of pick-off attachments can be set in degrees, using the numeric keypad.
Factory automation - The CS 2001 monitor has important auxiliary functions such as air pressure, lubrication pressure, and coolant pressure. In addition, output from the CS 2001 can be incorporated into your factory network via The LoganNet WiFi Module production and machine status.
Training - Operators can learn to operate a CS 2001 control within hours of installation.
5 Simple Ways to Improve Quality and Productivity
1. Thread Check
Improves Quality. Detects when the tap has cut to full depth. Taps last longer through positive clutch engagement/disengagement.
The Thread Check feature eliminates the possibility of producing parts that are not tapped. While in operation, the CS 2001 determines whether the tapping cycle is complete before high-point.
If the tapping cycle does not complete before high-point, the CS 2001 will immediately shut down the machine prior to indexing; eliminating the possibility of breaking the tap in the workpiece.
In addition to saving the tap and improving part quality, the Thread Check feature eliminates the additional hours of labor needed to sort through thousands of parts to identify whether they were actually tapped.
2. Machine Lock-Up Detection
The patented Clutch Saver™ feature detects machine lock-up in milliseconds, and shuts down the machine. Prevents damage to clutches and drive elements.
3. Programmable High Speed and Low Speed Shift Points
Reduces set-up time and improves cycle-time as much as 20%. Allows the operator to precisely set high and low speed shift points, maximizing tool position in relation to the workpiece, without having to re-time high speed and brake cams. This single feature can pay for your new CS 2001 within months.
4. Programmable Tool Change Counters
Reduces tool breakage and maintains high quality finish on parts. Allows for scheduled maintenance programs.
5. Simple integration of Door Interlocks
The machine will go into a jog mode if a door is opened while the main motor is running. This enables operators and set-up people to work in the tool zone, and jog the machine as required during setup; but prevents the main motor from running. Three levels of security in the software ensure supervisor - operator compliance.
Logan CS 2001TM Control Features and Benefits
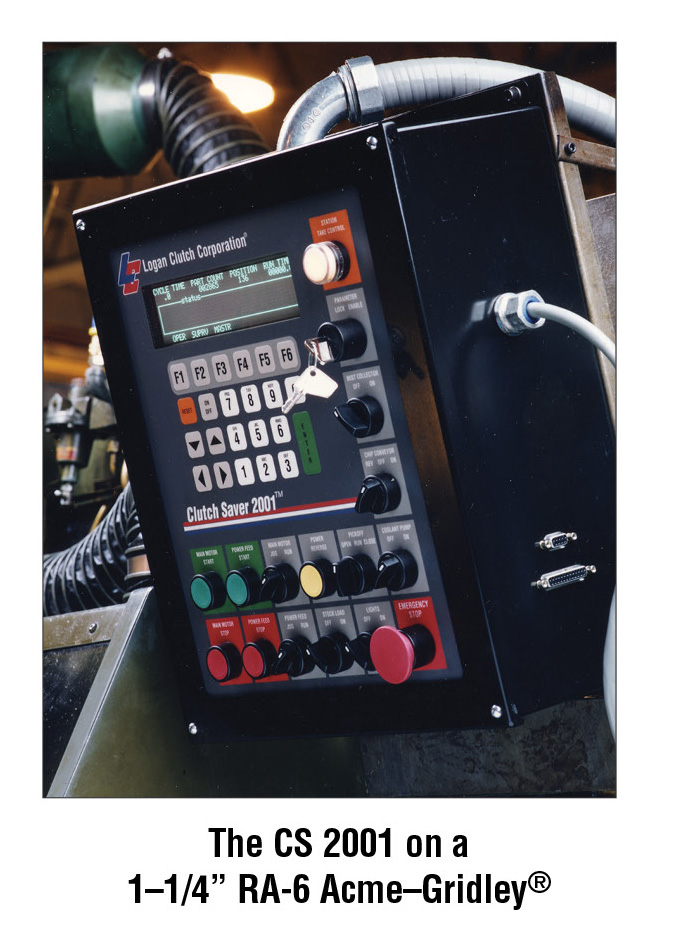
1. Machine Lock-up Detection: Greatly increases clutch life by detecting clutch slippage caused by machine lock-up; disengaging the clutch before damage occurs.
2. Programmable High Speed Shift Point: Allows the machine operator to program the high speed clutch engagement point, giving the operator more set-up flexibility.
3. Programmable Low Speed Shift Point: Allows the machine operator to program the feed clutch engagement point, which enables the operator to optimize the set-up without having to mechanically re-time the high speed and brake cams.
4. Programmable Pick-off Point: Enables the operator to program the pick-off engagement point in degrees; simplifies set-up and eliminates mechanical adjustment of cams.
5. High Point Stop Reference: Automatically stops the machine close to high point; useful during set-up.
6. Low Point Stop Reference: Automatically stops the machine close to low point; reducing set-up time.
7. Cycle Time Display: Displays the machine cycle time in seconds. Useful in detecting machine problems. Cycle time variation may indicate clutch slippage.
8. Revisable Parts Counter: Makes it possible to change the counter display. Useful during stock-up, enabling the operator to correct the parts count as needed.
9. Air & Lube Pressure Monitor: Senses below normal air & lube pressure and shuts down the machine.
10. RS 232 and RS485 Data Collection Ports: Collect cycle time, run time, parts count.
11. Coolant Pressure Monitor: Senses below normal coolant pressure and shuts down the machine.
12. Stock Depletion: Takes input from your device and shuts down the machine when the bar stock becomes too short to feed out to length.
13. Tapping Right Hand/Left Hand Select: Makes changing from right hand tapping to left hand tapping as easy as pushing a button.
14. Thread Check / Tapping Failure Detection: Shuts the machine down if the tapping cycle does not complete before machine index. Prevents parts without threads, sorting costs, etc.
15. Stock-up Mode: Automatically stops the machine in the correct position for material loading.
16. Programmable Air Blast: Allows the operator to program the exact time to blast air on the part for chip cleaning, or for part ejection versus a constant air flow; saving compressed air for other uses.
17. Alarm Message Display: Display gives descriptive message of any alarm or error message that occurs, or causes the machine to stop. Saves messages in series for diagnostic review.
18. Position Display in Degrees: The display screen lets the operator know where the machine is in the cycle.
19. Mist Collector/Chip Conveyor Control: Automatically shuts off the mist collector/conveyor after 3 minutes of non-run time. Minimizes coolant conveyed into the chip system.
20. Programmable Tool Change Counters: Shuts the machine down at designated tool service time; minimizing unnecessary tool changes and maximizing quality finishes and threads.
21. Five Auxiliary Outputs: Allows operator to program, in degrees, the engagement and disengagement point of attachments, such as thread rollers, into machine cycle. Eliminates auxiliary cams associated with attachments.
22. Simple integration of Door Interlocks: The machine will go into a jog mode if a door is opened while the main motor is running.
WARRANTY: CS 2001 Control hardware is warrantied for 6 months after installation, or 1 year after purchase. Field installation and service are not under warranty and are sold separately. Consult Logan for details of limited warranty. Specifications subject to change without notice.
Contact Our Sales Team
Our Sales Engineers can help you find the exact product or service you need to succeed.